China pneumatic air slide conveyor system for cement
China pneumatic air slide conveyor system for cement
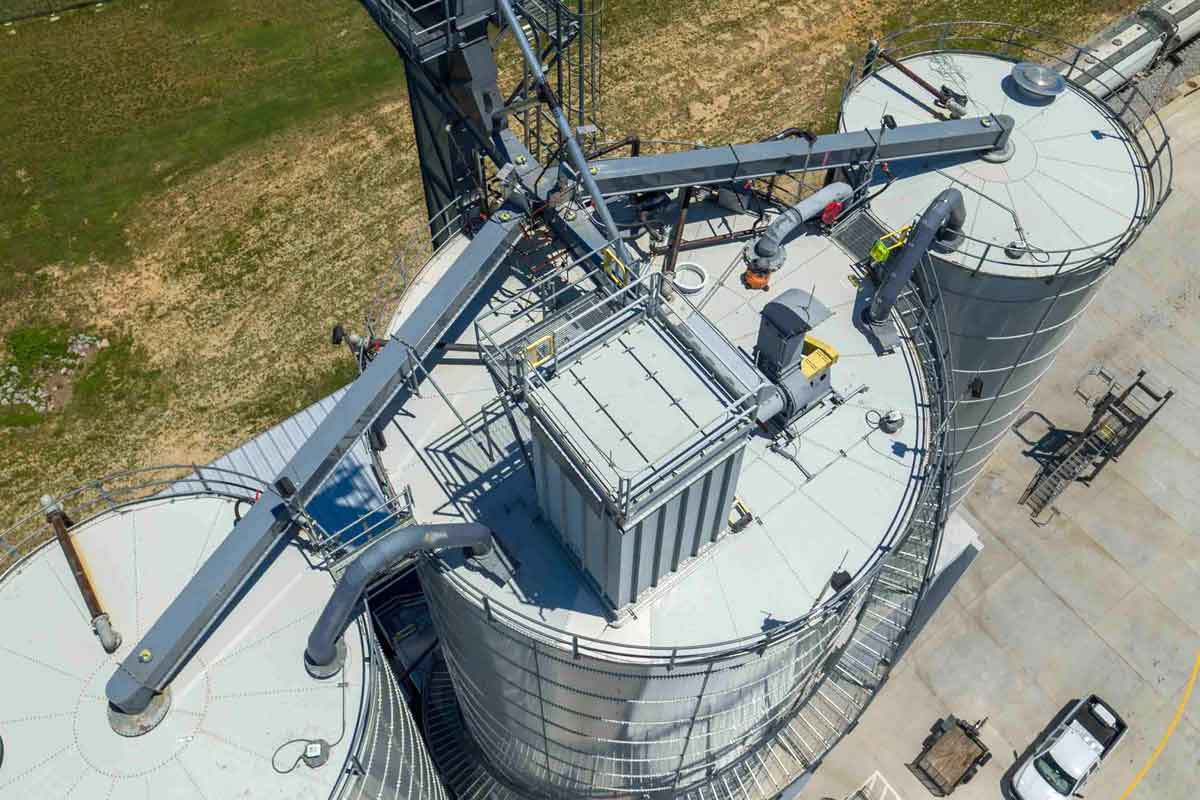
What is a air slide?
A air slide , also known as air slide conveyor ,pneumatic conveying airslides, air slide gravity conveyor, air slide conveyor system.
A air slide is a kind of pneumatic conveying equipment used for conveying dry powder materials, and it takes the fan as the power source, which makes the materials in the closed conveying chute flow slowly at the inclined end under the fluidization condition, the main part of the equipment has no transmission part, easy maintenance, good sealing, no noise, safe and reliable operation, less power consumption, convenient to change the transmission direction, and convenient to multi-point material feeding and multi-point material unloading.
Air slide are widely used in construction material industry,chemical industrial.
Technical Features:
1.Simple structure,easy to install and maintain, low production cost,and high cost-effective
2.Convey most dry powders such as cement,dry mortar ,fly ash,flour,starch, ect.
3.Convenient to change the transmission direction
4.Convenient to multi-point material feeding and multi-point material unloading.
5.Enclosed, dust-free
6.No damage to product handled (reduce waste)
7.No moving parts (reduce wear, spare parts & prolongs service life)
8.Low energy consumption
9.Low noise ,fan or blower is remote from the conveyor.
Features and scope of use
The air slide is a horizontal conveying equipment installed at an angle. The conveyed material flows from the high end to the low end in a fluid state. It is suitable for powdery materials that are easy to fluidize, such as cement and fly ash, but cannot transport materials with large particle size, large moisture content, and high density that are not easy to fluidize.
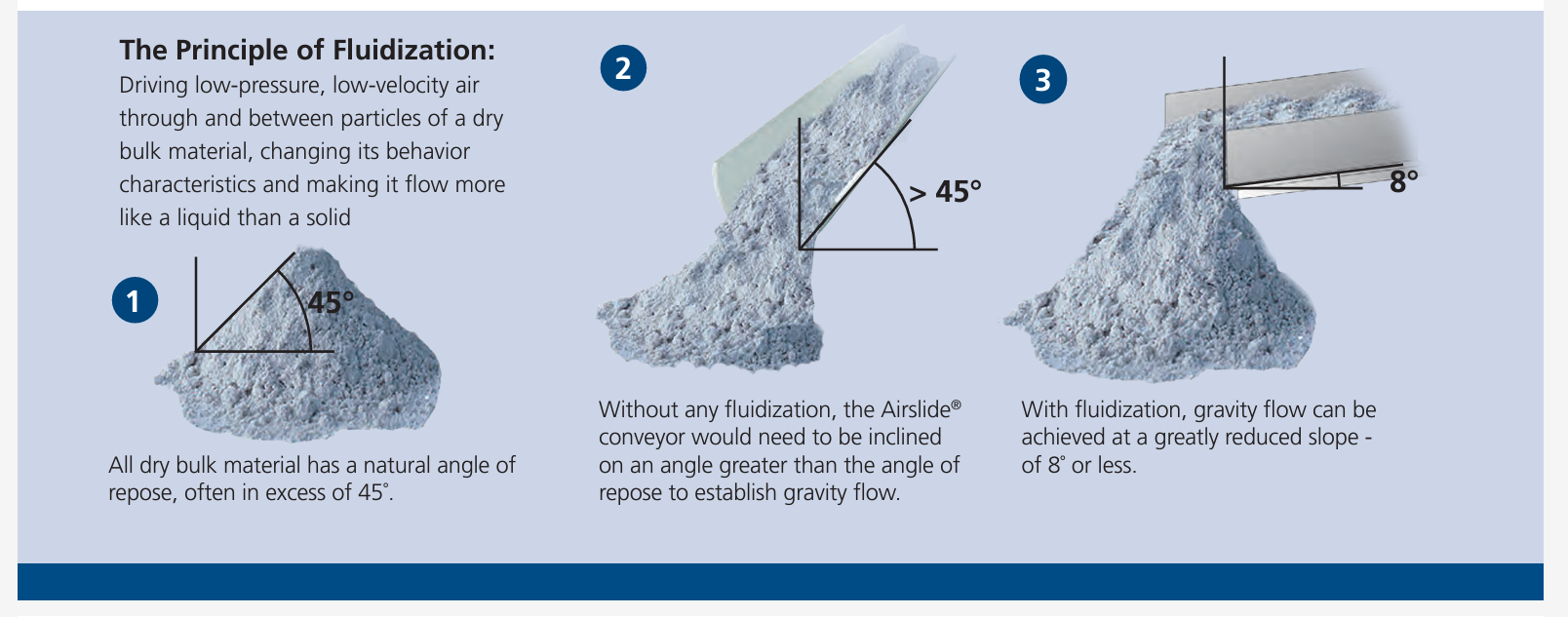
Air slide applications
Technical parameters
Model |
Conveying capacity (ton/hour) |
Max.power consumption (KW/10M) |
Air volume (m3/min/10m) |
DCS-200 |
45-70 |
0.6-1.6 |
3.0-8.0 |
DCS-250 |
70-110 |
0.8-2.0 |
4.0-10.0 |
DCS-300 |
105-160 |
0.9-2.5 |
4.5-12.50 |
DCS-400 |
160-260 |
1.2-3.2 |
6.0-16.0 |
DCS-500 |
260-400 |
1.5-4.0 |
7.5-20.0 |
DCS-600 |
400-680 |
1.9-5.0 |
9.5-25.0 |
DCS-800 |
680-1150 |
2.4-6.4 |
12.0-32.0 |
The above parameters are only for reference ,and it is subject to our final confirmation.
Working principle:
The high-pressure air pumped in by the blower enters the lower part of air slide from the air inlet through the air duct, the air diffuses to the upper part through the air-permeable layer, and the powder material transported enters the upper part, after the feed inlet enters the upper part, above the permeable layer is a gas flow with a certain velocity, filled with the gaps between the particles and a fluidization.Under normal conditions, the section of material layer is divided into four layers from bottom to top: fixed layer, gasification layer, flowing layer and static layer. Due to the inclined arrangement of the chute, the fluidized powdered material flows from high to low under the dual effects of gravity and airflow, and is finally discharged through the outlet
Technical parameters
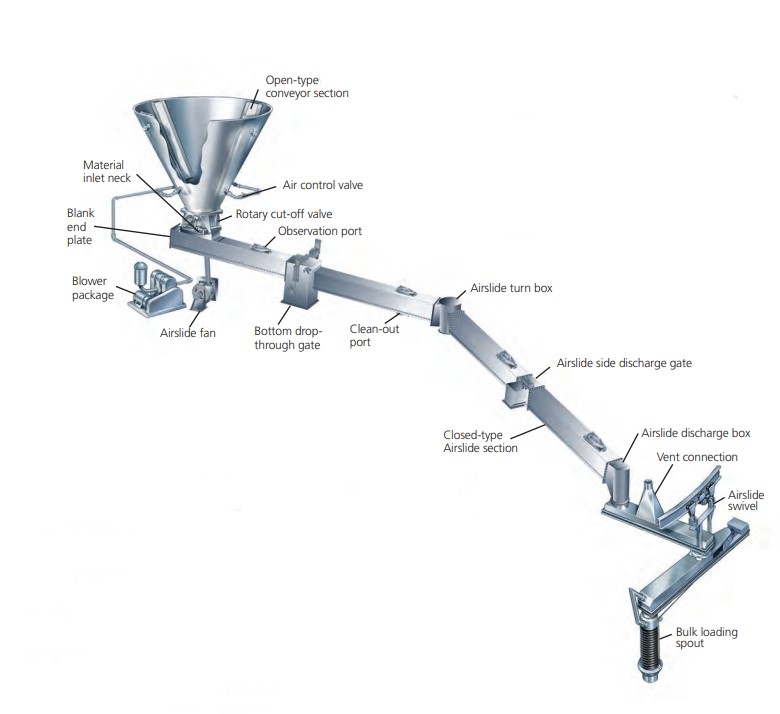
Structure
1. Upper and lower chute bodies: The chute body is generally made of steel plates pressed into rectangular sections, with a standard length of 2m or 3m for each section, and flanges made of flat iron at both ends.
2. Breathable layer: There are two types of breathable layers: new polyester breathable layer and porous board breathable layer.
3. Air inlet: The air inlet is composed of a cylindrical air duct connected to the bottom plate of the lower chute.
4. Feeding port: The feeding port is located on the top surface of the upper chute, which can be rectangular or circular. To reduce the impact force of the material and prevent the polyester fabric from being dented or damaged, a steel plate porous plate should be installed at the upper part of the breathable layer at the feeding port.
5. Discharge port: The discharge port is divided into the end and middle discharge ports. The middle discharge port is located on the side of the upper chute and is equipped with a plug plate for material blocking.
6. Gas shut-off valve: controls the amount of air used in the chute.
7. Observation port: located on the side of the upper chute, used to observe the flow of materials inside the chute.
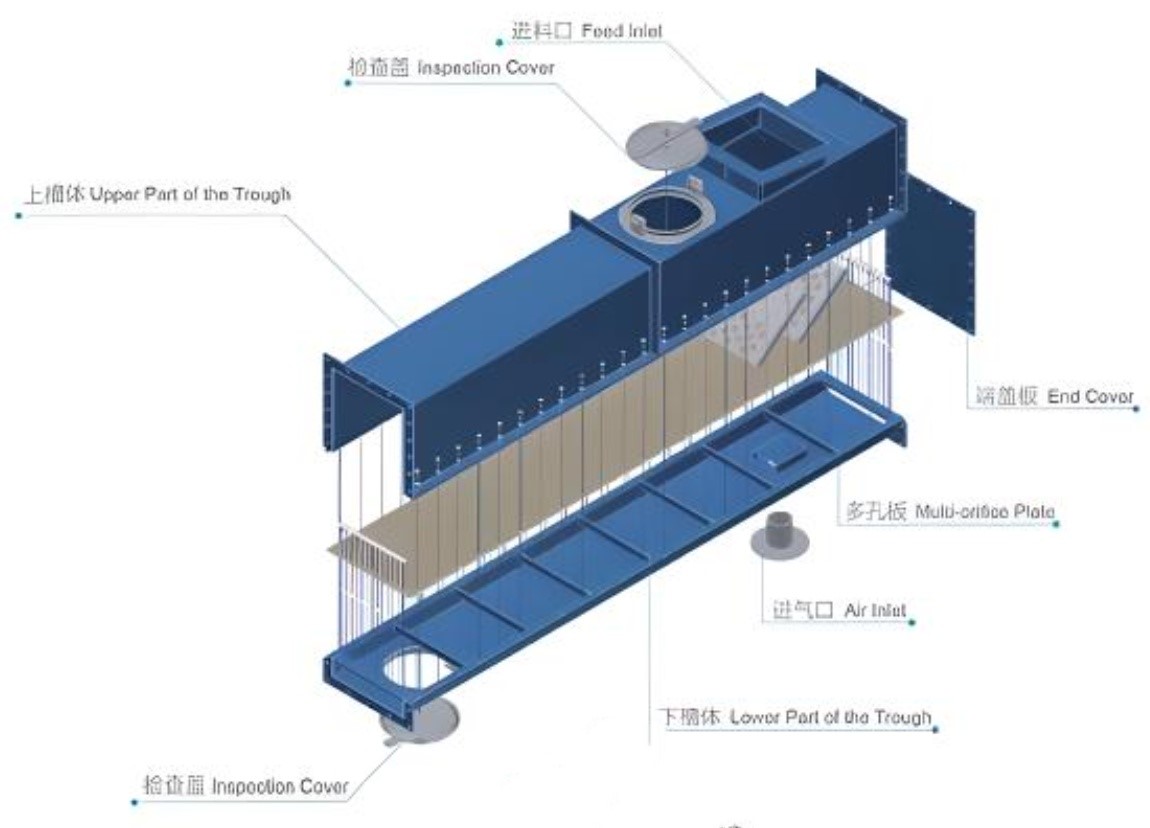
System Options:
Turn Boxes: Used to divert product flow.
Side Discharges: Allow materials to be diverted toward other processes between the beginning and end of an air-gravity conveyor.
Slide Gates or Drum Valves: Used to shut off and regulate material flow through the upper chamber.
Dust Collection Vent: Mounted at the end of the conveyor to collect fugitive dust.
Bin or Filter: In order to convey materials through an air slide conveyor, air is introduced and contained within the system. At some point, this air must be properly vented through a bin or filter within the system.
A systems analyst can advise if any of these options should be considered for a particular air-gravity conveying system.
Projects pictures for reference
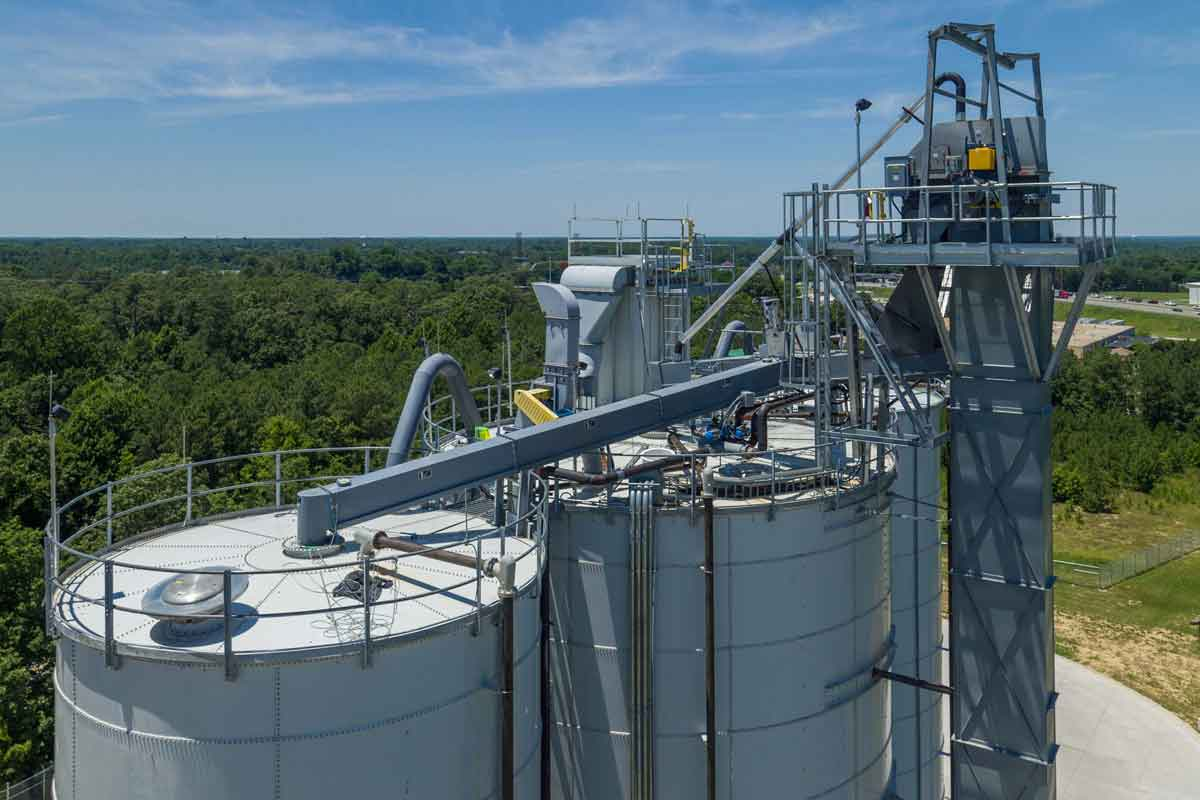
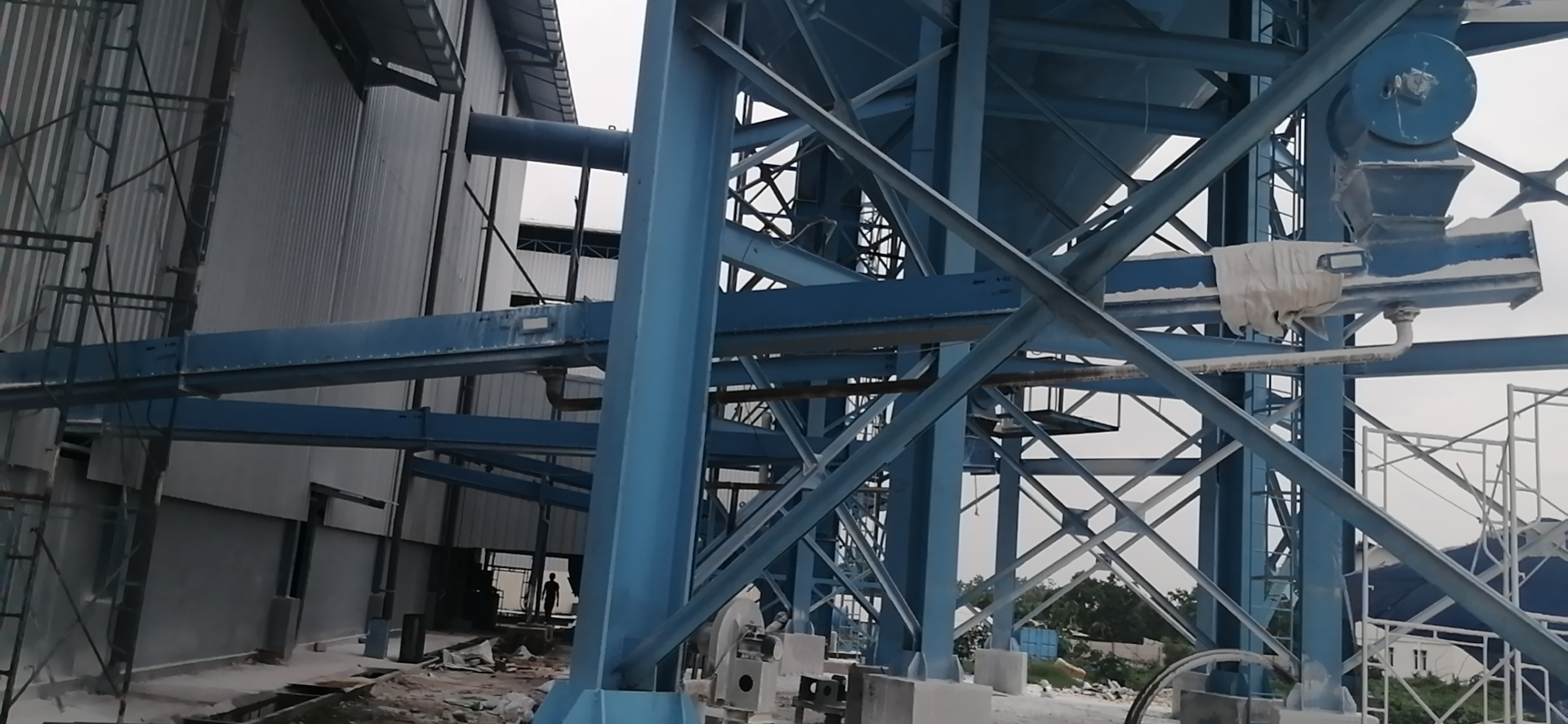
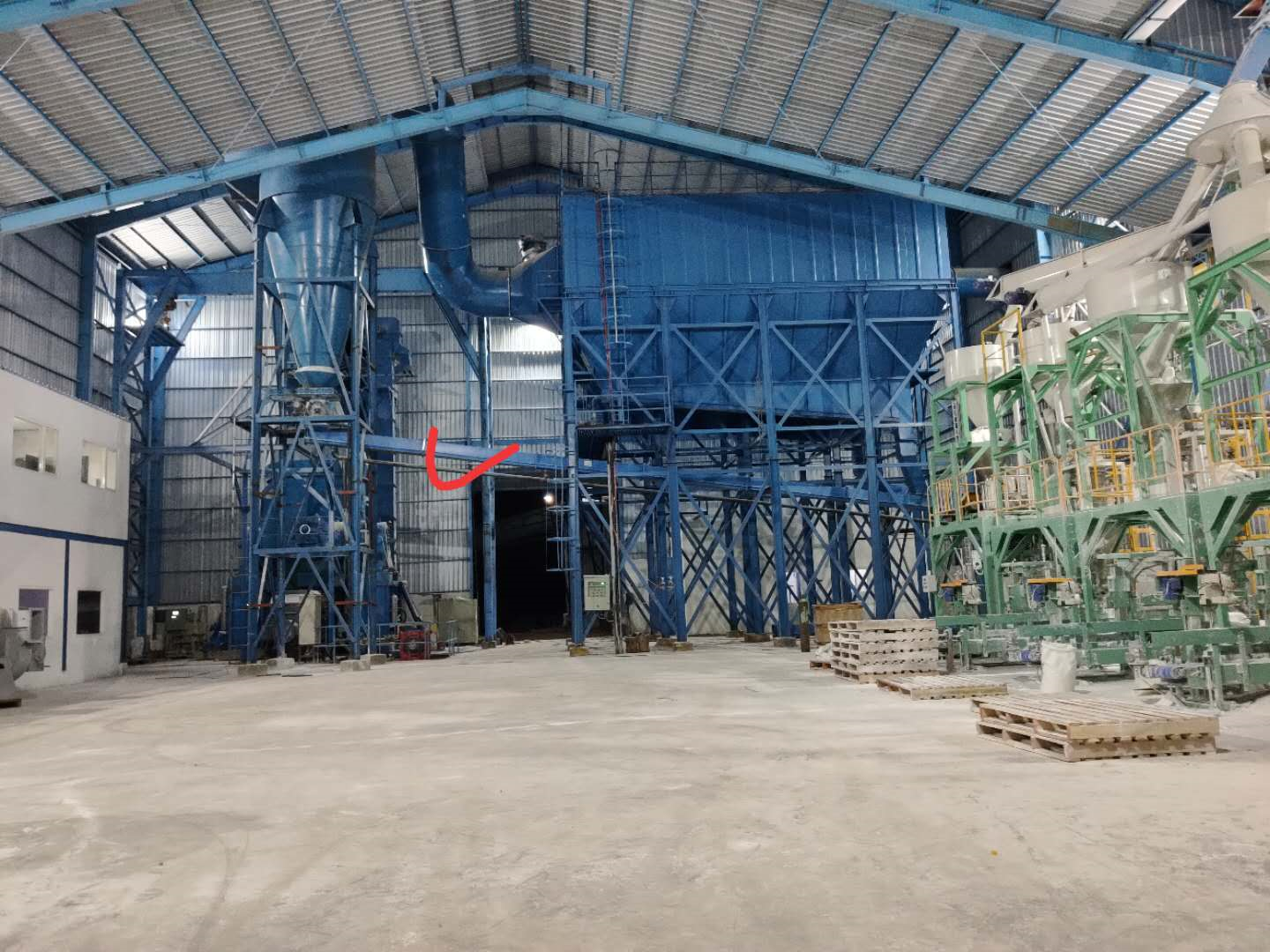
Mr. Yark
Whatsapp: +8618020515386
Mr. Alex
Whatsapp:+8613382200234